Centrifuges are common and important tools for the laboratory. Choosing the right rotor system for each centrifuge can maximize the equipment’s performance and longevity. In recent years, centrifuge rotor materials have progressed, and a wider range of options is now available. This rotor evolution gravitates toward lighter and stronger materials; rotor weight reduction increases ease of use, while stiffer rotors add strength and hold the structure together even under a rotor’s maximum load. The materials used in centrifuge rotor design continue to evolve; today, new improvements are realized through the use of composite materials, such as carbon fiber.
Traditional materials
Since the early 1950s, centrifuge rotors have been constructed mainly from metal alloys. Alloy was chosen primarily based on weight considerations, resulting in the long-established usage of lightweight aluminum and titanium metals in rotor manufacturing. Aluminum, having a low density, is a commonly used material for superspeed and benchtop centrifuge rotors. The greater structural properties of titanium are better suited for ultracentrifuge rotors, which experience the highest level of stress of all rotors. These metals, however, suffer from a number of well-known natural limitations, most notably their lack of resistance to corrosion, susceptibility to elongation, or elastic stretching generated by stress and undesirable mass.
Advances in technology
A significant innovation in the material technology of centrifuge rotors has been the introduction of carbon fiber composite materials. Some of the most demanding applications, including aerospace, military structures, wind turbines, and sports equipment, have increasingly turned to carbon fiber-reinforced composites. These composite materials have several highly desirable traits, addressing many of the limitations of their metal counterparts, while improving performance.
Lighter weight
Centrifuge rotors present a unique lifting hazard in the laboratory. Conventional floor-model centrifuge rotors can weigh up to 70 lb (~30 kg) when fully loaded. In addition, their awkward shape compounds the risk of strains during installation and removal from the centrifuge. Considering the substantial weight, a second person should always assist with the removal from the centrifuge, and a cart may be necessary for rotor transport.
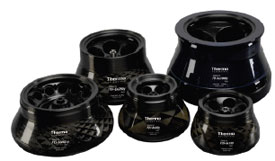
Figure 1 - A full range of carbon fiber rotors is available, all with significant weight and life span advantages.
Alternatively, carbon fiber rotors (see Figure 1) are lightweight, since the material has a higher strength-to-weight ratio than most metals. As a result, these rotors can be used to achieve higher levels of strength with less mass. For example, a midsize superspeed carbon fiber rotor may be 45% lighter than the equivalent aluminum rotor.
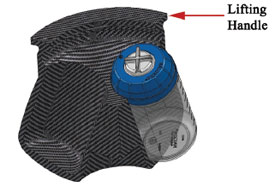
Figure 2 - Computer-aided design (CAD) cross-section of a rotor cell hole, showing the position of the built-in lifting handle.
These lightweight rotor designs also offer improved ergonomics, decreasing the likelihood of damage to the equipment during rotor installation or removal and contributing to a safer work environment. For example, most large-volume carbon fiber rotors are designed with a lifting handle (see Figure 2) at the top of the rotor. This allows users to transport the rotor in and out of the centrifuge with less force and bending, reducing the chances of lower back injury.
The lightweight properties also reduce the amount of inertia that must be overcome by the centrifuge drive system to turn the rotor. Faster acceleration and deceleration rates reduce overall run time, and the reduced stress on the centrifuge causes less wear to critical centrifuge drive components.
Corrosion resistance
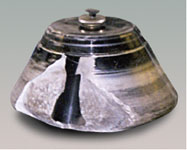
Figure 3 - The catastrophic failure of a rotor due to unchecked corrosion.
When selecting a rotor, the potential of the material type for stress corrosion is a critical consideration. Centrifuge rotors are often exposed to moisture, chemicals, or alkaline solutions such as sodium hydroxide or other salts in the laboratory, which may attack the surface. The resulting corrosion or pitting weakens the rotor’s structural integrity by reducing the amount of metal available to bear stress during operation (see Figure 3). This is traditionally the primary cause of failure of aluminum rotors, especially as they age. Titanium rotors are also susceptible to corrosion, and repeated use may weaken the structure. Any indication of surface damage to a rotor should be carefully examined by a service technician.
Unlike aluminum and titanium, which are prone to corrosion and pitting, carbon fiber is corrosion-resistant, thus eliminating an ever-present hazard. Not only are these rotors more forgiving to exposure of regularly occurring laboratory corrosives, such as most organic solutions, but they are also safe for use with most laboratory detergents and commercially available solutions for radioactive decontamination, which are highly alkaline.
Fatigue resistance
The high rotational speeds generating centrifugal force create load or stress on the rotor, with ultraspeed rotors experiencing the highest level of stress of all rotors. However, it is also an important consideration for lower-speed rotors, which also experience substantial g-forces.
Due to the tremendous forces, rotors are subject to stretching and change in size during centrifugation, a phenomenon called “elongation.” At a certain level of stress or after repeated cycles, the fluctuating stresses and strains cause fatigue or permanent structural damage in metal rotors, and they lose the ability to regain their original size and shape at the end of the run. These changes in structure generate microscopic cracks that enlarge with continued use and ultimately cause the rotor to fail. Maximum speed and sample density ratings published by rotor manufacturers are intended to prevent this type of damage. Additionally, most manufacturers publish recommended retirement guidelines for metal rotors based on a certain number of runs or hours. These guidelines limit the useful lifetime but are necessary to avoid a rotor failure.
The use of advanced composite materials enables longer life spans for rotors. Composite materials, including carbon fiber, are exceptionally resistant to fatigue and are increasingly used as replacements for many key industrial applications and products. Fatigue in carbon fiber rotors is a very slow process. This is due to less elongation in thermoset composite material and enables the life span of carbon fiber rotors to far exceed those of their metal counterparts.
A long-term investment
While rotors made from aluminum and titanium have been around for many years, advanced carbon fiber composites are quickly becoming the material of choice due to the many benefits mentioned. As a result, a wide variety of these rotors are available today ranging from ultraspeed and superspeed rotors for floor-standing models to general purpose and microcentrifuge rotors for benchtop centrifuges.
Carbon fiber rotors are used in some of today’s most demanding environments and are designed with similar dimensions as traditional rotors; thus it is not necessary to change centrifuge methods.
As an elite new material, there is often an assumption that a carbon fiber rotor will be more expensive than a rotor made from traditional metal alloys. This is not necessarily the case. Carbon fiber has quickly spread over several thousands of applications from its origins as a material of the aerospace industry. This transformation has generated a rapidly growing network of resources, which has supported further advancement in the industry, but has also reduced cost as improved processes are developed.
Finally, it is important to realize that the investment is a longer-lasting one and that each laboratory will make an informed decision that will serve the needs of today and for many years to come.
Ms. Piramoon is Product Manager, Thermo Scientific Fiberlite Rotors, Thermo Fisher Scientific, 422 Aldo Ave., Santa Clara, CA 95054, U.S.A.; tel.: 866-9THERMO; e-mail: [email protected].